Introduction:
In today's rapidly evolving world, industries heavily rely on work truck trailers for the transportation of goods, materials, and equipment. These trailers play a crucial role in ensuring the smooth operation of businesses across various sectors, including logistics, construction, and agriculture. However, like any other equipment, work truck trailers are subjected to wear and tear, resulting in potential breakdowns and costly repairs. To mitigate these risks, the implementation of predictive maintenance strategies has gained significant attention. This article explores the concept of work truck trailer predictive maintenance, its benefits, challenges, and how it can revolutionize the industry for a sustainable future.
1. Understanding Predictive Maintenance:
1.1 Definition and Objectives:
Predictive maintenance refers to a proactive maintenance strategy that leverages data, analytics, and advanced technologies to predict equipment failures before they occur. The primary goal of predictive maintenance in work truck trailers is to optimize their performance, reduce unplanned downtime, and extend their lifespan.
1.2 Key Components:
Predictive maintenance relies on various components, including data collection, condition monitoring, data analysis, and decision-making systems. These components work together to provide real-time insights into the trailer's health, enabling informed maintenance decisions.
2. Benefits of Predictive Maintenance for Work Truck Trailers:
2.1 Cost Reduction:
Predictive maintenance helps minimize unexpected breakdowns, reducing the need for emergency repairs and associated costs. By identifying potential issues in advance, maintenance activities can be scheduled during planned downtime, optimizing resources and personnel.
2.2 Increased Efficiency:
Regular monitoring and analysis of trailer conditions enable early detection of issues, allowing for timely repairs or replacements. This ensures that work truck trailers operate at optimal efficiency, reducing fuel consumption, and maximizing productivity.
2.3 Enhanced Safety:
Work truck trailers subjected to predictive maintenance are less likely to experience sudden failures or malfunctions, contributing to improved road safety. By addressing potential safety hazards promptly, the risk of accidents and injuries is significantly reduced.
2.4 Extended Equipment Lifespan:
By proactively managing the maintenance needs of work truck trailers, predictive maintenance helps extend their lifespan. Identifying and addressing minor issues before they escalate minimizes wear and tear, ultimately reducing the need for premature equipment replacement.
2.5 Sustainability:
Predictive maintenance aligns with sustainable practices by optimizing resource utilization. The reduction in unplanned downtime and emergency repairs decreases the environmental impact associated with excessive energy consumption, waste generation, and carbon emissions.
3. Implementing Predictive Maintenance for Work Truck Trailers:
3.1 Data Collection and Monitoring:
To implement predictive maintenance effectively, a robust data collection and monitoring system is essential. This involves equipping work truck trailers with sensors and IoT devices to capture relevant data, such as temperature, pressure, vibration, and other performance indicators.
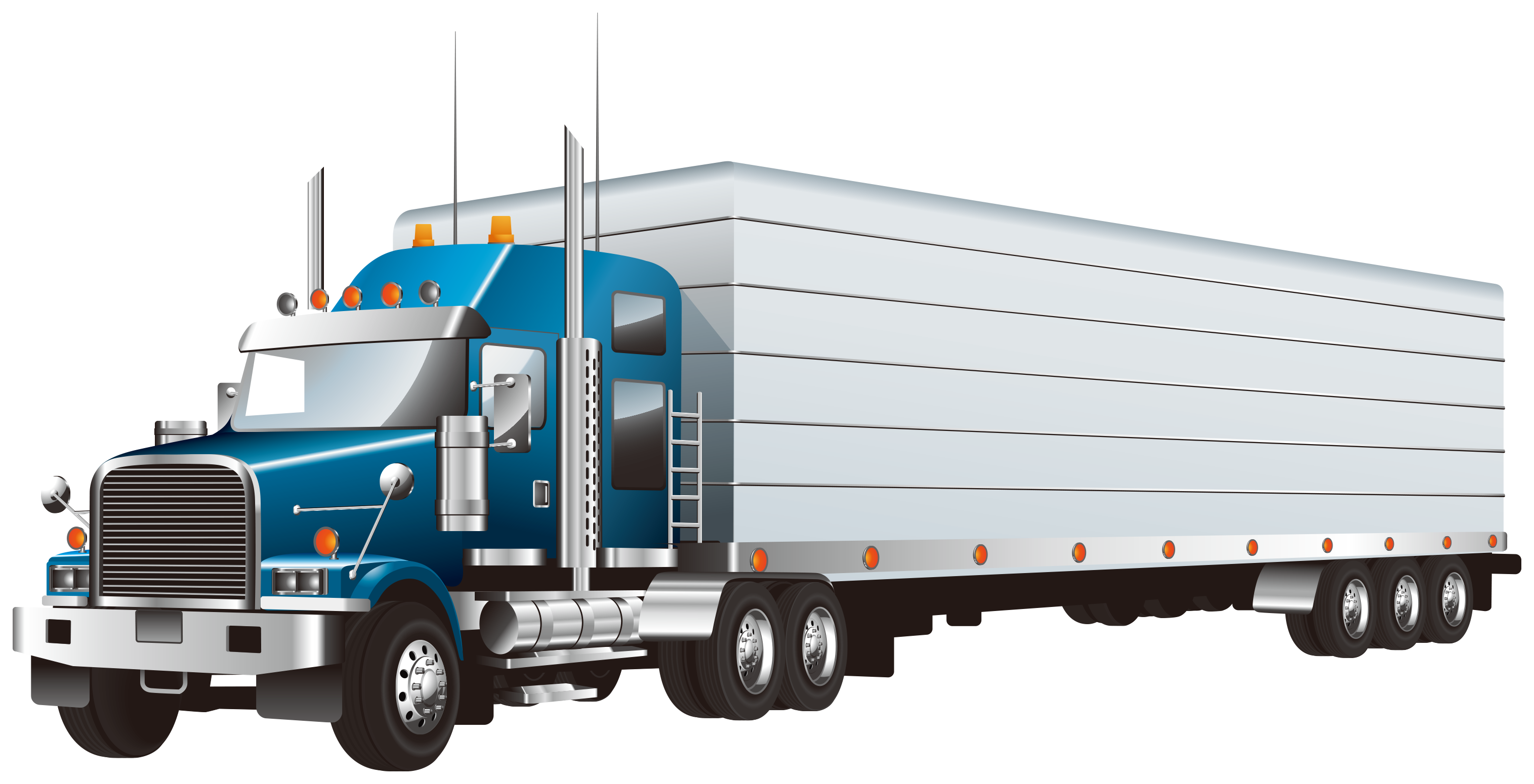
3.2 Data Analysis and Predictive Modeling:
The collected data is then analyzed using advanced analytics techniques, such as machine learning algorithms and artificial intelligence. These models identify patterns, anomalies, and potential failure modes, enabling accurate predictions of maintenance needs.
3.3 Integration with Fleet Management Systems:
Integrating predictive maintenance systems with fleet management platforms allows for seamless monitoring and analysis of work truck trailers' health. This integration enables real-time notifications, alerts, and maintenance scheduling based on the analyzed data.
3.4 Training and Skill Development:
Successful implementation of predictive maintenance requires skilled personnel who can interpret the data, make informed decisions, and perform necessary maintenance activities. Providing training and skill development opportunities to the workforce is crucial for maximizing the benefits of predictive maintenance.
4. Challenges and Considerations:
4.1 Data Quality and Integration:
The accuracy and reliability of predictive maintenance systems heavily rely on the quality and integration of data from various sources. Ensuring consistent data collection and integration across different work truck trailers and fleet management systems is a significant challenge.
4.2 Cost and Return on Investment (ROI):
Implementing predictive maintenance systems and equipping work truck trailers with sensors and IoT devices may require significant upfront investment. A thorough cost-benefit analysis is necessary to assess the potential return on investment and justify the adoption of predictive maintenance strategies.
4.3 System Scalability and Compatibility:
As businesses expand their fleets and embrace new technologies, scalability and compatibility become critical considerations. Predictive maintenance systems should be able to handle increasing data volumes and integrate with evolving fleet management platforms and technologies.
4.4 Workforce Acceptance and Training:
Introducing predictive maintenance practices may face resistance from the workforce due to fear of job displacement or unfamiliarity with new technologies. Proper change management and comprehensive training programs are vital to foster acceptance and ensure successful adoption.
5. Case Studies and Success Stories:
5.1 Company A: Implementing Predictive Maintenance for Fuel Efficiency:
Company A, a logistics provider, implemented predictive maintenance strategies on its work truck trailers to optimize fuel efficiency. By monitoring tire pressure, wheel alignment, and engine performance, they reduced fuel consumption by 10% and extended tire lifespan by 20%, resulting in substantial cost savings.
5.2 Company B: Enhancing Safety through Predictive Maintenance:
Company B, a construction company, integrated predictive maintenance systems with their fleet management platform to ensure the safety of their work truck trailers. By monitoring https://www.worktruckmaker.com/changan-new-energy-pure-electric-cargo-van-box/ , suspension, and trailer stability, they reduced accidents by 30% and improved driver satisfaction.
6. Conclusion:
Work truck trailer predictive maintenance is transforming the way industries manage their fleets, ensuring efficiency, reliability, and sustainability. By leveraging data, analytics, and advanced technologies, businesses can proactively address maintenance needs, reduce costs, enhance safety, and extend the lifespan of their work truck trailers. While challenges exist, the potential benefits and success stories highlight the importance of embracing predictive maintenance strategies for a sustainable future in the transportation industry.